How to Install Metal Roofing Over Shingles
There are billions of square feet of commercial and industrial roofing applications in the United States, and much of it requires repair. Installing metal roofing over existing shingles is an excellent way for contractors to help building owners maximize the longevity of their new roof while saving them money (not to mention the headaches!) of roof tear-off.
Why Install Metal Roofing Over Existing Shingles?
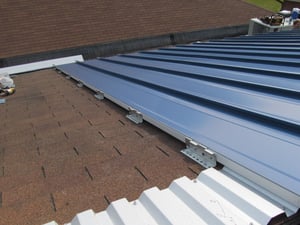
Shingles might be inexpensive roofing material, but they require maintenance and frequent replacement. Consequently, many owners simply tire of the constant expense, mess, and disruption to their business operations. Metal roofing offers building owners a way out of the shingle replacement cycle.
Metal roofing typically requires a more significant up-front cost than new shingles, but metal roofing can last 50+ years with minimal maintenance. (That’s easily 2-3 times the life expectancy of a shingle roof!) A metal roof also adds curb appeal to a building because they come in a vast variety of styles and colors.
Longevity and aesthetics aside, metal roofing is made from recycled material and is 100% recyclable at the end of its lifespan. So for building owners looking to be environmentally friendly, it’s tough to find a more eco-friendly roofing option than metal panels. Shingles are rarely recycled, and because waste disposal companies and landfills receive so many shingles, they often charge a large fee to accept them.
In contrast, installing a metal roof over existing shingles means that any shingle tear-off expenses, including disposal fees, are avoided entirely. Additionally, you gain all the benefits of a metal roof.
Want to learn more about the differences between metal roofing and shingles? Check out this article from our partner S-5!
Metal Roofing Over Existing Shingles Options
Once you’ve decided to stop the constant churn of shingle replacement and use metal panels instead, it’s time to determine the specific installation method you plan to use. There are a few basic approaches when using metal roofing over existing shingles. Let’s explore the most common.
Metal Panel Attachment into Furring or Lathing Strips
In this scenario, wood purlins or sub-girts are used as furring strips on the old roof and attached to the structure below. This framing system can be installed directly over existing shingles or applied over existing decking or underlayment. The new metal roof panels are then attached to the framing system.
The image above illustrates a general furring strip approach, although, as you might guess, there are numerous variations to this method. This method typically involves less mess than a complete tear-off.
However, with the added cost of the furring material and installation, the final price can be similar to tear-off. Although, it is undoubtedly more environmentally friendly since the shingles remain in place. This approach does add some weight to the roofing system, so it’s essential to determine if the structure can support the additional weight.
For more on this technique, check out this white paper by the Metal Construction Association.
When using this approach, it’s important to remember that the copper elements in pressure-treated wood may aggressively attack metal panels. Consequently, if using pressure-treated lumber for furring applications, a barrier of #30 felt or synthetic underlayment should be used between the wood framing and metal panels.
Metal Panel Attachment Directly into Shingles
One of the most cost-effective installation methods involves attaching metal panels directly through the shingles and into the wood deck below. While this method saves the cost and labor of furring strips, it’s important to remember that steel often acts as a mirror and can telegraph deck and shingle inconsistencies through the metal panels.
While this condition is purely aesthetic and doesn’t affect panel performance, homeowners with a high emphasis on aesthetics may be better suited with a remove-and-replace approach or a system like our 138T, which we will address a bit later.
There are a couple of additional considerations with the direct attachment approach. First, it’s challenging to achieve Above Sheathing Ventilation (ASV) with this installation method. ASV is critical to reducing energy consumption.
You can learn more about ASV here.
Consequently, while this approach often represents the most economical installation, it also offers reduced energy savings.
Second, it’s important to note that a barrier between the original shingles and the new metal roof is required for direct attachment projects. This layer of protection is critical to prevent the shingles from wearing through the metal panels as they expand and contract over the roof’s life. Common barrier products include #30 felt, synthetic underlayment, or even thin foil-faced insulation.
Shingle Recover Systems
A third recover approach involves using our patented 138T Shingle Recover System. This system avoids the cost and labor required by the furring strip approach mentioned earlier. Further, the clip design maximizes the system’s appearance. But perhaps most importantly, it provides ASV or an Above Sheathing Ventilation airspace, which helps owners maximize energy savings.
Additionally, the panels in this system are symmetrical. Conversely, many other types of standing seam panels are asymmetrical. While there is only one letter different in these two words, the implications during roof installation and ownership through the roof’s life are much more significant than that one letter might imply.
Symmetrical systems (like our 138T) can be installed and replaced in any order. In contrast, asymmetrical systems require installation in a predetermined manner (commonly left to right). Should repair or replacement become necessary during the roof’s life on an asymmetrical system, the same arduous left to right process is required. In fact, it's not uncommon to be forced to remove perfectly good panels to access those that need to be repaired or replaced when working with asymmetrical style roof panels. When this occurs, repair costs and scrap generated can both be significantly higher than what would be anticipated with symmetrical panel systems.
In contrast, repair or replacement is effortless with symmetrical systems since contractors can simply start the repair or replacement at the specific point of concern.
Click here for an animation highlighting the components of the Shingle Recover System.
Learn More about Installing Metal Roofing Over Shingles
If you are interested in learning more about replacing your shingle roof with metal roof panels, we’re here to help.
- Check out some of our recover projects in our photo gallery.
- Download our popular eBook, Tired of Replacing Your Shingle Roof? Why Business Owners & Institutions Choose Metal Roofing
- Check out case studies on some of our recent recover projects:
- Use the Find a Contractor feature on our website to find an experienced installer near you to get a quote for your project.
- Whether you’re a contractor already working with our team at McElroy Metal or are interested in using our products for your next project, contact us today to learn more or become part of our national network of distributors and contractors.
About McElroy Metal
Since 1963, McElroy Metal has served the construction industry with quality products and excellent customer service. The employee-owned components manufacturer is headquartered in Bossier City, La., and has 14 manufacturing facilities across the United States. Quality, service and performance have been the cornerstone of McElroy Metal’s business philosophy and have contributed to the success of the company through the years. As a preferred service provider, these values will continue to be at the forefront of McElroy Metal’s model along with a strong focus on the customer.
Comments on this article:
Scroll down to the bottom to submit a comment and join the conversation. Need help or have a question? Please contact us. Looking for a distributor or contractor? Please click here to get started.