Anyone who invests in a metal roof expects to see the benefits they were promised. Long life, low maintenance, looks great, no color fade. These are just a few of the benefits buyers expect.
If the metal roof exhibits an effect commonly known as oil canning some building owners perceive that the value of the metal roof goes down. But should that really be the case? Let’s dig into the facts about oil canning.
What is oil canning?
Oil canning is something you see when a metal panel appears wavy or distorted. Oil canning is an inherent characteristic of cold-rolled flat metal panels. It only becomes an issue if the effect is highly visible to the naked eye as someone looks at a metal roof.
Oil canning may occur with any metal roofing substrate including steel, copper, zinc, and aluminum. It is most commonly an issue with standing seam roof systems. The color of the roof, roof finish, roof pitch, temperature, sunlight, season, and the angle the viewer is to the roof all play a part in the appearance of the oil canning effect.
Oil canning, if seen, does not indicate quality or structural issues with the roof. Instead, it is purely a visual appearance phenomenon.
What causes oil canning?
Determining the root cause of oil canning is difficult to definitively identify.
Possible causes include:
- Deviations in the roof sub-structure
- Twisting the panel excessively during installation
- Over-driving fasteners
- Movement of the underlying structure
- Uneven stresses at the fastening points
- Temperature variation along the roof (usually when one part is in direct sunlight and another in the shade)
- Installing wider panel widths
- Issues with the rolling process at the mill including poorly adjusted or worn roll formers
- Distortions introduced during the slit or forming process
Considerations during product selection to minimize oil canning in a metal roof
Because it’s purely aesthetic, oil canning isn’t a concern in many building applications. But for high-slope or high-visibility projects where oil canning would be problematic, there are some steps that can be taken during the product selection phase to reduce the phenomena of oil canning.
It is possible to introduce oil canning during the panel manufacturing process. So it’s incredibly important to select a panel manufacturer with trained technicians who understand the importance of ensuring that equipment is properly maintained and calibrated before production begins. For this reason, some specifiers do not allow panels to be site-formed. Others will allow panels to be produced on-site but include rigorous quality standards in their specifications regarding operator training and machine maintenance.
To minimize the effect of oil canning, panel widths can also be reduced. Standing seam panels are typically 12-24” wide. Since oil canning is more common in wide/flat areas, it’s logical to assume that panel widths of 24” would be the more prone to oil canning. So going to a narrower panel width can certainly help. With that said, going to narrower panels typically comes with both a higher material and install price as contractors are handling more panels and accessories so installation time is slower.
In some applications, using a heavier gauge material can also help reduce the effect of oil canning. Consequently, it’s not uncommon for design professionals to require 22 gauge panels instead of the standard 24 gauge material. While this too can be effective, the heavier material comes with a higher price tag that can increase the cost of the roofing system.
Because both of the aforementioned approaches come with a higher cost, a more common practice is to put some sort of configuration in the panel during the roll forming process. Striations, minor ribs and planks are all widely available from most reputable manufacturers. Not only are they highly effective, they are typically offered at no additional cost. And depending on the roof slope, eave height and color of the roof, they may not even be visible after installation. Consequently, the addition of some slight configuration in the panel is the most common and cost effective approach to minimize the effect of oil canning.
Things to do during installation to minimize oil canning in a metal roof
Like many things in life, the best defense is a good offense. For projects where oil canning is a concern, the installation crews play a critical role. And their responsibilities (and ability to cause oil canning) start when they receive the material at the job site.
Panels should not be carried flat or lifted by a single corner from a bundle or crate. Instead, installers should always follow the manufacturers handling and installation procedures.
It’s also important to remember that steel acts as a mirror and can literally reflect whatever is below it. Consequently, before any panels are installed, it’s critical to ensure the deck is level, plumb, and free of imperfections. An experienced crew foreman also understands the importance of planning the layout and start point of a run to avoid inducing stress which can inadvertently cause oil canning.
Installing a backer rod under the panel is another common method to reduce oil canning. It puts a very slight "bow" into the panel which removes the appearance of waviness.
Bottom line: Crews should watch for oil canning throughout the project installation. If any effects are noticed, installation crews stop installation immediately and contact their Project Manager.
In summary, it’s important to remember that oil canning is purely an aesthetic issue and does not impact the structural integrity or life expectancy of a metal roof project. With that said, it can be troublesome to building owners so designers working on projects with metal roofs should always consult with a manufacturer to discuss job specific approaches to reduce the possibility.
Learn more
You may be interested in these other posts about metal roofing:
- How to Walk on Metal Roofs
- What is the Best Underlayment for a Metal Roof?
- Can You Attach Solar Panels to a Metal Roof?
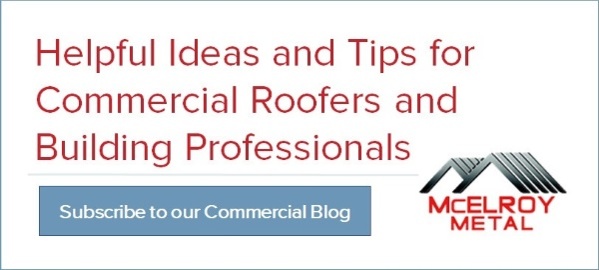
About McElroy Metal
Since 1963, McElroy Metal has served the construction industry with quality products and excellent customer service. The employee-owned components manufacturer is headquartered in Bossier City, La., and has 14 manufacturing facilities across the United States. Quality, service and performance have been the cornerstone of McElroy Metal’s business philosophy and have contributed to the success of the company through the years. As a preferred service provider, these values will continue to be at the forefront of McElroy Metal’s model along with a strong focus on the customer.
Comments on this article:
Scroll down to the bottom to submit a comment and join the conversation. Need help or have a question? Please contact us. Looking for a distributor or contractor? Please click here to get started.